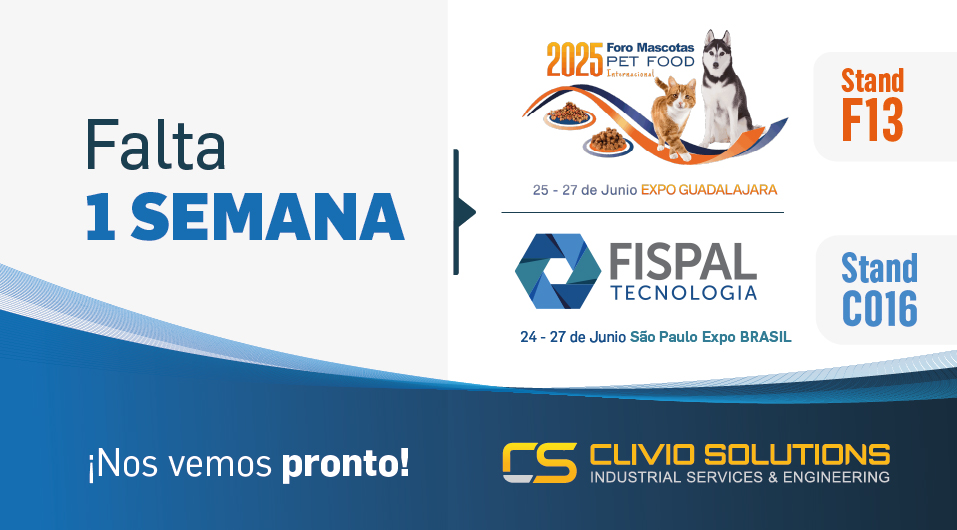
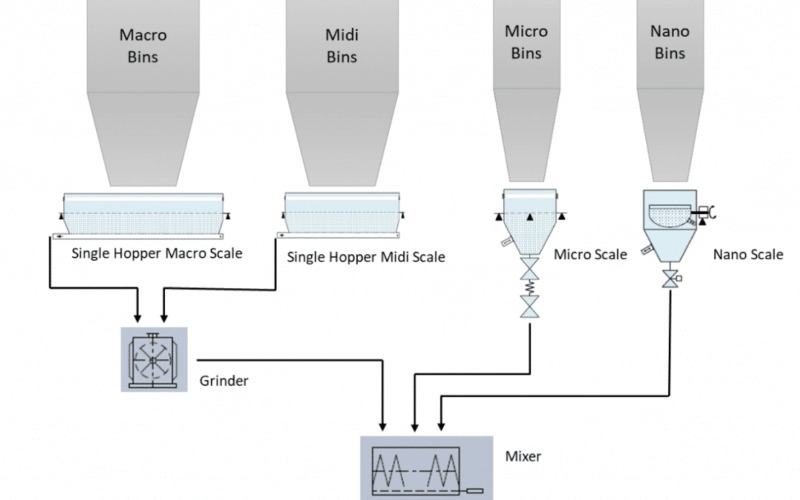
How to Improve Accuracy on your Macro and Midi Ingredient Weighing Systems?
Scales and Weighing Systems
Animal feed production is a typical example of a discontinuous production process that employs both discontinuous and semi-continuous operations. The bottleneck in many feed factories is the macro and midi dosing cycle. This bottleneck can be avoided by employing a Jesma solution, which optimizes both the dosing operation and the dosing accuracy at the same time.
Included in the Typical Animal Feed Factory
Focusing on a balanced animal feed factory process, you will find the dosing, weighing, and mixing process. A dosing system typically operates at an average of about 10-12 batches/hour, corresponding to 5-6 minutes per batch. When calculating the total processing time per batch, it is necessary to include the emptying of the scales and transport systems.
The typical feed factory includes a macro scale, a midi scale, a micro scale, and a nano scale.
Calculating Total Batch Processing Time
When calculating the total batch processing cycle time, the following operations must be included:
- Dosing (each ingredient is dosed one by one).
- Scale stability between each dosing.
- Emptying of residues and transferring ingredients to the next step of the process.
- Resting time for emptying the transport line.
To avoid cross-contamination between different batches and production orders, the scale and transport lines must be cleaned by running the chain conveyors and bucket elevators for some time after the last product has been unloaded from the hopper scales.
As mentioned earlier, a typical batch processing cycle in a feed factory is 5-6 minutes, and the bottleneck in many feed factories is the macro and midi dosing cycle. To eliminate this bottleneck, Jesma has developed solutions that optimize both the dosing operation and the dosing accuracy.
Option One: Replacing the Simple Macro-Midi Scale with a Double Hopper Scale
The single hopper macro and midi scale can be replaced with a double hopper scale. The advantage of this solution is that it allows two operations to be performed simultaneously: dosing in the weighing container (each ingredient dosed one by one) and at the same time emptying the subsequent container. The time saved by this solution is approximately 40-70 seconds, which is equivalent to the time it takes to empty the macro/midi scale and transfer the batch to the next step. In most cases, this solution will also improve dosing accuracy.
Option Two: Installing Smaller Scales on Top of the Single Hopper Scale
In some cases, it will be possible to install one or more smaller scales on top of a single hopper scale. This allows for dosing more than one ingredient at a time, reducing dosing time and simultaneously improving the accuracy of dosing for the given ingredient. The time saved with this solution is approximately 10-15 seconds per small scale for a single ingredient installed.
Other Options to Increase Batch Processing Speed
These could include:
- Increasing the size and/or speed of the dosing apparatus (screw feeder or similar dosing device).
- Increasing the capacity of the transport lines used to transfer the batch from the scale to the next step of the process.
The other options mentioned above will not benefit from increased weighing accuracy and, therefore, are not considered best practices.